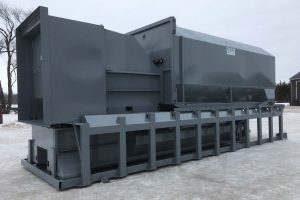
Solutions We Offer
Rotobale’s line of compactors and recycling equipment have been designed and engineered to achieve maximum container loads. Through this, our customers are able to realize immediate and long-term cost savings by reduced haulage and tipping fees. Additionally, customers are able to achieve a positive impact to their overall carbon footprint.
How do we pack more? Through 40 years of compaction experience, with all common types of commercial and food service refuse, we have developed and applied a unique range of compaction principles into the design of our equipment.
Ram Penetration – Rotobale maximizes ram penetration into the container. With stroke depths from 14”-18”, Rotobale’s equipment has one of the highest penetration rates in the industry.
Ram Design – With a slightly smaller ram face and lower ram height, our compaction force is maximized. In addition, the lower ram height maximizes the chute slope, improving the flow of refuse into the mouth of the compactor.
Load Dwell – At the end of the forward compaction stroke, the ram will pause and dwell against the load to ensure that the refuse is held in its compacted state long enough to minimize spring-back and produce a tightly packed load.
Safety First! – As a core value of Rotobale Compaction Solutions, safe operation of our equipment is first and foremost. The design of our compactors and cardboard balers has been independently audited for full compliance with the latest safety standards. We believe our products are the safest in the industry.
Fast Utilization – An advantage of our third party safety review is that Rotobale’s compaction and baling equipment installed by a qualified technician can be used without incurring a delay while the Pre-Start Health and Safety Review Exemption and Approved for Use/Production certificate is obtained, saving you time and money! Talk to Rotobale about how our compaction and baling equipment can be configured so you can use it right away.
Maximize Loads –Ideal when waste volume varies week to week, Rotobale’s optional RFID system notifies your hauler automatically when your container reaches 3/4 capacity. This eliminates costly scheduled pick-ups of part container loads as it ensures container “fullness” every time. Through the use of RFID technology, signals are automatically sent to the hauler as either an email or a text message. Minimizing the amount of human intervention required means no more missed fullness indicators. Hauler service levels can be accurately tracked and measured against submitted invoices.
Over four decades of product design and installations have proven that no two installations are the same. Optimizing the equipment selection is only the beginning. Designing and installing the best in-feed for your application takes experience and the mandate to do what’s right; not just sell ‘what’s on the shelf’.
At Rotobale, we offer a variety of basic in-feed designs as a starting point. Our design review shows you what’s possible, exploring all options and opportunities to make the final solution more efficient. For example, through-the-wall chutes and walk-on enclosures offer alternatives for simplifying access and for ease of sorting recyclable materials.
From this point, each installation is designed and manufactured in Rotobale’s facilities ensuring accuracy when it arrives at your site.
These components turn your waste handling solution into an extension of your existing building, freeing up floor space and optimizing the safe management of waste or recyclables.
Count on Rotobale to help you select the best equipment and installation configuration to serve your immediate and future needs.
Rotobale understands the importance of having the right equipment onsite and operational as soon as possible. As such, our compactors and balers are designed to allow for installation in one day – minimizing your downtime, inconvenience and additional costs associated with having temporary bins.
When you purchase a Rotobale compactor or baler, you are purchasing a total package of end-to-end responsive support, including:
Our site consultation service is your best assurance that you are acquiring the optimal solution to suit your requirements and site conditions. With our experience in manufacturing and installing a wide range of compaction systems since 1968, Rotobale has the expertise to customize a feed application to suit your requirements.
All deliveries and installations are coordinated by Rotobale to coincide with customer priorities and any other on-site conditions such as removal of old equipment, electrical connection, pad pressure washing and/or parking lot paving.
On completion of the installation by our qualified technicians, all equipment is fully tested. Demonstration and training is provided to ensure that your staff who will be operating the equipment has a thorough understanding of safe and proper procedures.
The justification is typically determined by the dollar savings and equipment payback time frame. A ratio is used to compare the uncompacted waste against the compacted waste. Savings are achieved through fewer pickups as a result of the compacted waste. The annual savings are then used to determine the equipment payback time-frame. If the savings and payback are favorable then the equipment is justified.
The type of compactor required depends on the type of waste product being generated by the client. For wet waste high volume a self-contained compactor would be recommended. For dry waste high volume a stationary compactor would be recommended. For wet or dry waste low volume a vertical compactor would be recommended. For cardboard waste a stationary compactor or vertical baler would be recommended.
The size of compactor required depends on the physical size and volume of the waste product being generated. The amount of space available would also need to be taken into consideration. The size of baler depends on the amount of cardboard being generated. Also the ceiling height is a factor when determining the size of baler required.
The safeguarding of all Rotobale compactors and balers has been reviewed and approved by a 3rd party safety engineering firm. Category 4 safety interlock switches are provided for feed applications with doors, lids, covers and gates. Equipment ships with a pre-start health and safety review and approved for use/production certificates.
Rotobale offers a full line of vertical balers, stationary, self-contained and vertical compactors.
Just write down some details and a Rotobale team member will get back to you soon!